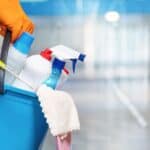
Looking for a Janitorial Cleaning Service Provider? Consider these 7 Factors
October 7, 2024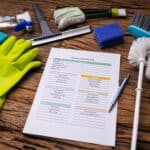
How Do You Set Up a Master Cleaning Schedule for Schools?
December 13, 2024Unplanned downtime is a common challenge for industrial facilities, and it comes with a hefty price tag — averaging around $125,000 per hour, according to 2023 surveys.
Each season brings its own set of challenges to facility operations. While summer months test equipment with heat stress and cooling demands, winter presents a unique combination of threats, from sudden power outages to transportation disruptions and equipment freezing. These factors can quickly lead to costly unplanned downtime if not addressed effectively.
Although completely eliminating unplanned downtime is impossible, proper preparation for the season’s unique challenges, including proactive preventative maintenance, can significantly reduce those challenges’ impact. With winter fast approaching, we thought it’s a good opportunity to share a comprehensive “Winter Checklist” to help keep your facility running smoothly.
Are you winter-ready?
US&S’s Full Winter Checklist for Industrial Facilities
To make sure no important system or area of your facility is left unaddressed, we divide our winter preparedness checklist into four main areas:
1) Interior Preparation
Your facility’s interior systems are the backbone of its operations, and winter’s harsh conditions can quickly expose vulnerabilities in your infrastructure. Proactive inspection and maintenance of critical indoor systems can prevent minor issues from escalating into major operational disruptions, mitigate unplanned downtime, and also aid in cost savings.
- HVAC Systems
-
-
- Inspect and service HVAC equipment
- Verify thermostat, humidity, and temperature control functionality
- Inspect air vents, air filters, blowers, and hoses for damage; Replace as needed
- Clean out drain lines and pans
- Test humidity and temperature controls
- Get more HVAC maintenance tips
-
- Power & Electrical Systems
-
-
- Inspect and test backup power systems and generators; Refuel as needed
- Verify electrical hookups and leads
- Install/check surge protectors
- Repair or replace exposed wiring
-
- Plumbing
-
- Ensure pipe insulation and wrap as needed
- Install leak detection sensors in flood-prone areas
- Seal cracks and openings around exposed pipes
- Check and test valve and shutoff operations
2) Exterior Preparation
Maybe even more than your facility’s indoor environment, the external environment faces direct potential damage from winter’s most challenging conditions. Securing the building’s exterior can help prevent accidents and minimize weather-related disruptions.
- High-Traffic Areas Preparation (parking lots, entryways, loading docks, and stairs)
-
-
- Apply slip-resistant tape
- Apply deicing materials (rock salt, gravel)
- Install safety mats and appropriate signage
- Repair concrete surfaces from cracks and holes
-
- Structural Preparation
-
- Clean out roofs and gutters
- Seal all windows and doors
- Inspect trees and power lines; Remove potentially hazardous branches
- Assess and improve exterior lighting
3) Essential Supply Preparation
Resource management is another crucial part of a comprehensive winter preparedness checklist. Having the right supplies can make the difference between a minor inconvenience and a complete operational shutdown — so let’s stock up.
- Stock drain cleaners
- Provide extra winter protective clothing (coats, gloves, hats)
- Secure snow removal equipment (shovels, snow blowers)
- Ensure fuel and deicing supplies
- Prepare first-aid and emergency preparedness kits
- Prepare an emergency vehicle
- Ensure your CMMS is updated with the latest equipment data, maintenance schedules, and winter-specific tasks to streamline tracking and response efforts
- Review and update snow removal service contracts
4) Emergency Plan
No matter how well-prepared your facility might be, you must be prepared for the worst to minimize the impact of unplanned downtime. With a solid emergency plan, you can avoid potential chaos and, instead, execute a coordinated action that protects your facility, your team, and your operational capabilities.
- Establish an emergency response team: Clearly define team members’ roles and responsibilities
- Maintain updated contact information for employees, vendors, partners, and clients.
- Develop detailed protocols for different emergency events
- Educate and train employees on these protocols
Winter Readiness Done Right
Preparing your facility for winter prevents disruptions, enhances energy efficiency, ensures smoother operations, and reduces the risk of costly disasters. By following this comprehensive winter checklist, you can confidently tackle winter’s unique challenges and maintain peak performance throughout the colder months.
If you’re looking for additional support, we’re here to help. Our O&M services provide expert guidance to ensure your facility is ready for any condition. Contact us today to request a free consultation and take the first step toward making your facility winter-ready.