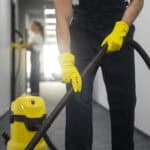
Post-Construction Cleaning for Commercial Spaces
April 8, 2025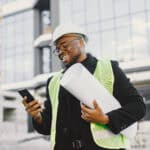
Building Management: Key Strategies & Tips
May 14, 2025Occupational Safety and Health Administration (OSHA) compliance is vital for maintaining a safe and productive work environment. For employers and managers across various industries, understanding and adhering to OSHA regulations not only ensures a safer workplace but also helps avoid penalties and fines.
In this guide, we’ll walk through what OSHA compliance is, cover a general OSHA compliance checklist, and share sector-specific tips for compliance.
What Is OSHA Compliance?
OSHA compliance refers to the set of federal regulations established by the Occupational Safety and Health Administration to ensure the safety and health of workers in the United States. These standards apply to virtually all industries, including healthcare, manufacturing, construction, and more. Compliance means employers adhere to the necessary safety protocols, risk assessments, and reporting requirements to safeguard their employees’ well-being.
Key Elements of OSHA Compliance
OSHA compliance is a broad category, but there are key elements every employer should address to maintain a compliant workplace. These typically include adherence to safety standards, employee training, proper reporting and documentation, and regular audits. While each business may tailor its OSHA compliance efforts based on industry and specific workplace conditions, it’s important to ensure all these areas are effectively covered.
OSHA Compliance Checklist
A comprehensive checklist can help ensure your business meets OSHA requirements, keeping your workplace safe and compliant.
1. Identify Workplace Hazards
- Conduct a thorough risk assessment: Identify potential physical, chemical, biological, and ergonomic hazards in your facility.
- Check environmental factors: Assess risks related to air quality, lighting, noise levels, and temperature.
- Focus on worker tasks: Review each employee’s work duties for any potential risks specific to their role.
2. Maintain Safety Equipment and Machinery
- Routine inspections: Develop a schedule for equipment maintenance and machinery inspections.
- Repairs and replacements: Ensure timely repairs or replacements of any damaged or faulty equipment.
- Testing: Regularly test emergency equipment (e.g., alarms, fire extinguishers, exit lights) to ensure proper functioning.
- Calibration: For specialized equipment, ensure regular calibration to maintain accuracy and safety.
3. Establish Safety Protocols and Procedures
- Create clear safety guidelines: Develop written protocols for emergency procedures, safety practices, and equipment use, and review periodically to account for any changes in the workplace.
- Establish emergency plans: Conduct fire drills, evacuation drills, and other emergency simulations to keep employees prepared.
- Ensure accessibility: Make sure emergency exits and routes are clearly marked and accessible at all times.
- First aid readiness: Ensure that first aid kits are fully stocked and easily accessible in case of emergencies.
- Promote communication: Maintain an open line of communication between employees and managers to report any safety concerns.
4. Provide Safety Training for Employees
- Onboarding training: All new employees should receive safety training before starting their duties.
- Ongoing education: Offer refresher courses and training sessions regularly to ensure workers stay updated on best practices.
- Specific training for tasks: Ensure employees receive training for any specialized equipment or dangerous materials they may encounter.
- Emergency response training: Make sure employees know how to react in emergencies, such as fires or chemical spills.
5. Ensure the Proper Use of Personal Protective Equipment (PPE)
- Assess PPE needs: Identify which roles or tasks require PPE (e.g., gloves, goggles, hard hats, respiratory protection).
- Provide adequate PPE: Ensure PPE is available, well-maintained, and accessible for all employees.
- Train employees on PPE use: Employees should know how to properly use, store, and dispose of PPE.
- Regular checks: Regularly inspect PPE to ensure it is in good condition and replace worn or damaged equipment.
6. Ensure Proper Ventilation and Lighting in the Workplace
- Ventilation systems: Check that ventilation systems are working effectively to prevent the buildup of hazardous gases or fumes.
- Adequate lighting: Ensure all areas, especially those with machinery or high-risk activities, are well-lit.
- Air quality monitoring: Conduct air quality checks in areas where chemicals are used or where workers may be exposed to harmful substances.
7. Document All Injuries, Illnesses, and Safety Incidents
- Maintain detailed records: Document all workplace injuries, illnesses, near misses, and safety incidents.
- Incident investigations: When an incident occurs, conduct a thorough investigation to determine the root cause and implement corrective actions.
- File reports: OSHA requires that certain incidents (e.g., fatalities and severe injuries) be reported within specific timeframes.
8. Conduct Regular Safety Audits and Inspections
- Audit safety systems: Perform regular safety audits to evaluate compliance with OSHA standards and identify areas for improvement.
- Inspect high-risk areas: Pay extra attention to areas with known hazards, such as machinery rooms, chemical storage areas, or construction zones.
- Track progress: Use audit findings to create action plans for improving workplace safety and compliance.
OSHA Compliance for Specific Sectors
OSHA compliance is essential across various sectors, but different industries may have specific requirements. Here’s a brief look at OSHA compliance in some of the most critical sectors:
Healthcare Facilities
OSHA compliance is especially important in healthcare environments to protect workers from biohazards, exposure to infectious diseases, and physical strain. OSHA compliance for dental offices and hospitals includes proper sanitation practices, sharps disposal, and infection control. Additionally, healthcare workers need training on handling medical equipment safely and minimizing the risk of exposure to harmful substances like chemicals or radiation.
Industrial Facilities
Industrial workplaces face unique safety risks, including heavy machinery, chemicals, indoor vehicles, and hazardous environments. OSHA’s standards for industrial facilities focus on equipment maintenance, worker training, and the proper handling of hazardous materials. Adhering to these guidelines can prevent accidents, injuries, and health-related issues in the workplace.
Other Sectors
Other industries, such as construction, retail, and agriculture, also have sector-specific OSHA standards. The key to staying compliant is to understand the specific risks in your sector and implement tailored safety programs that address these hazards.
How US&S Can Help You Stay OSHA Compliant
At US&S, we specialize in providing tailored solutions to help businesses across multiple sectors stay compliant with OSHA standards. Whether you’re in healthcare, industrial facilities, or another sector, we can help you implement safety programs that meet OSHA regulations.
If you need assistance with OSHA compliance or other safety-related services, don’t hesitate to contact us for expert support and solutions.