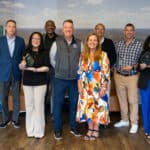
US&S Awarded 2024 SRNS SDVOSB Supplier of the Year
February 4, 2025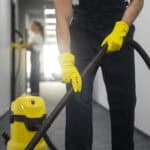
Post-Construction Cleaning for Commercial Spaces
April 8, 2025Checklists are great. They provide clarity, they are organized, and they are user-friendly. It’s no surprise the Internet is flooded with so many checklists for any need, industry, or project (including this very blog, for instance, our winter preparedness checklist for industrial facility managers).
However, in industrial settings, a maintenance checklist is not enough. Facility maintenance demands a broader perspective, one that views your facility as a living, interconnected system. Just like the human body, where every organ and system works in harmony, your facility relies on the synergy of its parts. When one system fails, it can trigger a cascade of issues that disrupt operations.
The Flaws of a Checklist-Only Approach
Imagine yourself being in charge of a simple office renovation project. Equipped with a checklist, you mark off tasks as you go through. Painting walls, replacing carpets, updating lighting. Seemingly perfect. It makes everything much easier. But what happens when you miss the critical connections between those tasks?
Over time, you notice the new carpet’s adhesive interacts poorly with the wall paint, causing gradual discoloration. The new flooring has a slightly different thickness than the previous one, making it impossible to close the door properly. All those “incompatibilities” that result from a narrow view of each task individually, eventually lead to costly, inconvenient hassles. These issues can also reflect poorly on the organization, making the brand appear unpolished.
What does it look like in industrial facilities?
Similar issues can arise in industrial facilities. A facility maintenance checklist might cover HVAC, plumbing, electrical, and other systems, but siloed thinking can create critical blind spots. For instance, low-flow plumbing fixtures might conserve water but increase sediment buildup in pipes, leading to leaks over time. Similarly, upgrading HVAC for energy efficiency could lower indoor humidity, inadvertently causing wooden materials to warp. This can lead to even more significant safety risks, as seemingly minor issues like warped flooring or bubbling floor paint can become major liability concerns. Can you imagine a forklift or any other machinery driving over those floors?
These problems don’t stem from neglect but from failing to view the facility as a dynamic ecosystem; From treating upgrades as separate tasks rather than as interconnected pieces of a larger whole. A facility manager with an ecosystem mindset would evaluate how each upgrade impacts other systems, ensuring compatibility and avoiding costly surprises.
Three Core Pillars of Facility Maintenance Ecosystem
1. Core Maintenance Strategies
Every well-maintained facility relies on foundational strategies to keep operations running smoothly. These strategies are proactive, data-driven, and reactive when necessary.
* Preventative Maintenance
Preventative maintenance is a proactive approach to facility maintenance that aims to reduce and even prevent breakdowns, downtime, and costly repairs. Examples include routine HVAC filter replacements, lubricating moving parts, CMMS software updates, plumbing inspections, etc. Having a preventative maintenance checklist in place is essential, but it must account for its impact on overall facility operations to avoid unintended issues.
* Predictive Maintenance
By leveraging data and analytics, predictive maintenance enables facility managers to anticipate potential issues before they fully develop. Sensors and monitoring tools analyze data over time, identifying subtle performance degradations in real-time and alerting teams to address problems at an early stage. This strategy transforms maintenance from guesswork to precise, data-driven, cost-effective decision-making.
* Corrective Maintenance
Even with preventative and predictive measures, issues can arise. Corrective maintenance focuses on repairs or replacements when something goes wrong. Addressing these issues promptly minimizes disruptions and restores operations as quickly as possible.
2. Infrastructure & Systems Maintenance
A facility’s infrastructure and physical assets form the foundation of its operations. Proper care and monitoring of these elements ensure long-term functionality and efficiency.
* Building Systems
These include maintaining all the “invisible” systems that are essential to the facility’s daily functions — from HVAC and lighting to plumbing and electrical. A tailored preventative maintenance checklist should be created for each system to ensure seamless and optimal performance.
* Physical Assets
Structural components, machinery, equipment, and furnishings are all part of an industrial facility’s physical assets, and they too, require consistent care. Equipment maintenance, in particular, is critical in preventing malfunctions and accidents. Regular maintenance of physical assets not only safeguards operational efficiency but also promotes a safe and reliable work environment.
3. Protection & Compliance
Compliance with health, safety, and environmental standards is a central aspect of modern facility maintenance. It ensures the well-being of occupants while minimizing the facility’s environmental impact.
* Sustainability
Beyond meeting regulatory requirements, a sustainable approach to facility maintenance offers numerous benefits. Implementing environmental and ecological best practices (such as energy-efficient systems and waste reduction programs) supports cost-saving through reduced electricity bills, prevents workers’ absenteeism, and enhances the facility’s reputation.
* Cleaning & Housekeeping
A clean facility is a productive facility. Routine cleaning and housekeeping efforts maintain a healthy, safe, and organized workspace, reducing accidents and pest infestations. Beyond aesthetics, cleanliness impacts employee morale and the overall perception of the facility.
* Health & Safety
Creating a culture of safety awareness helps facilities prevent accidents, ensure regulatory compliance, and protect their most valuable asset — their people. This involves practices such as regular inspections, risk assessments, and employee training, including fire drills.
Building an Ecosystem Mindset in Facility Maintenance
To adopt an ecosystem mindset in facility maintenance, it is essential to concentrate on two principles.
First, shift from a reactive, task-oriented mindset to a proactive, big-picture approach. This means looking beyond immediate “maintenance checklist items” and considering the long-term operational efficiency of the facility as a whole. Proactive maintenance involves anticipating how each decision impacts the larger system, reducing risks, and ensuring sustainability.
Second, foster cross-department collaboration. Maintenance teams can no longer work in isolation; they need strong communication channels with IT, operations, finance, and safety departments. For example, when maintenance identifies a potential equipment issue, they should engage IT to assess technological implications, involve operations to gauge productivity impacts, and consult finance to evaluate long-term cost considerations.
This collaborative mindset promotes knowledge-sharing and alignment between departments, leading to smarter, more cohesive decision-making and a truly interconnected facility management strategy.
Partnering for Success
Facility maintenance is evolving from a series of disconnected tasks to a sophisticated, interconnected ecosystem. Understanding these relationships is no longer optional, but essential for operational excellence.
At US&S, we understand the importance of maintaining this holistic approach. As a trusted partner in facility maintenance, we offer vendor consolidation — a single-source solution for all your facility needs. From operations and maintenance (O&M) solutions to janitorial services, we’re here to support your facility’s ongoing success. Explore our comprehensive services today, and contact us to learn how we can help streamline your facility management efforts.